What to consider when life sciences is part of a mixed use scheme
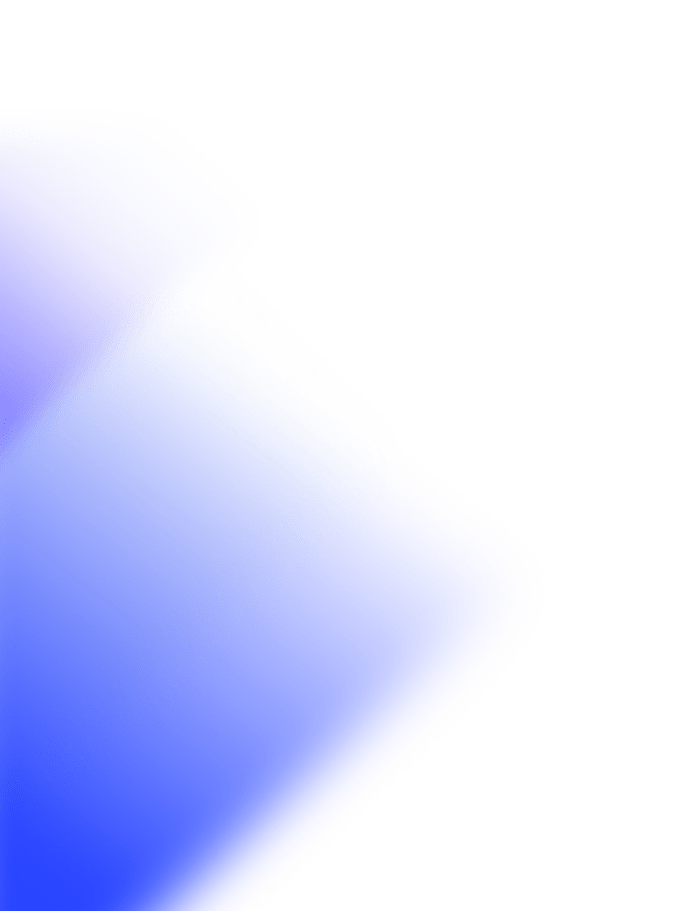
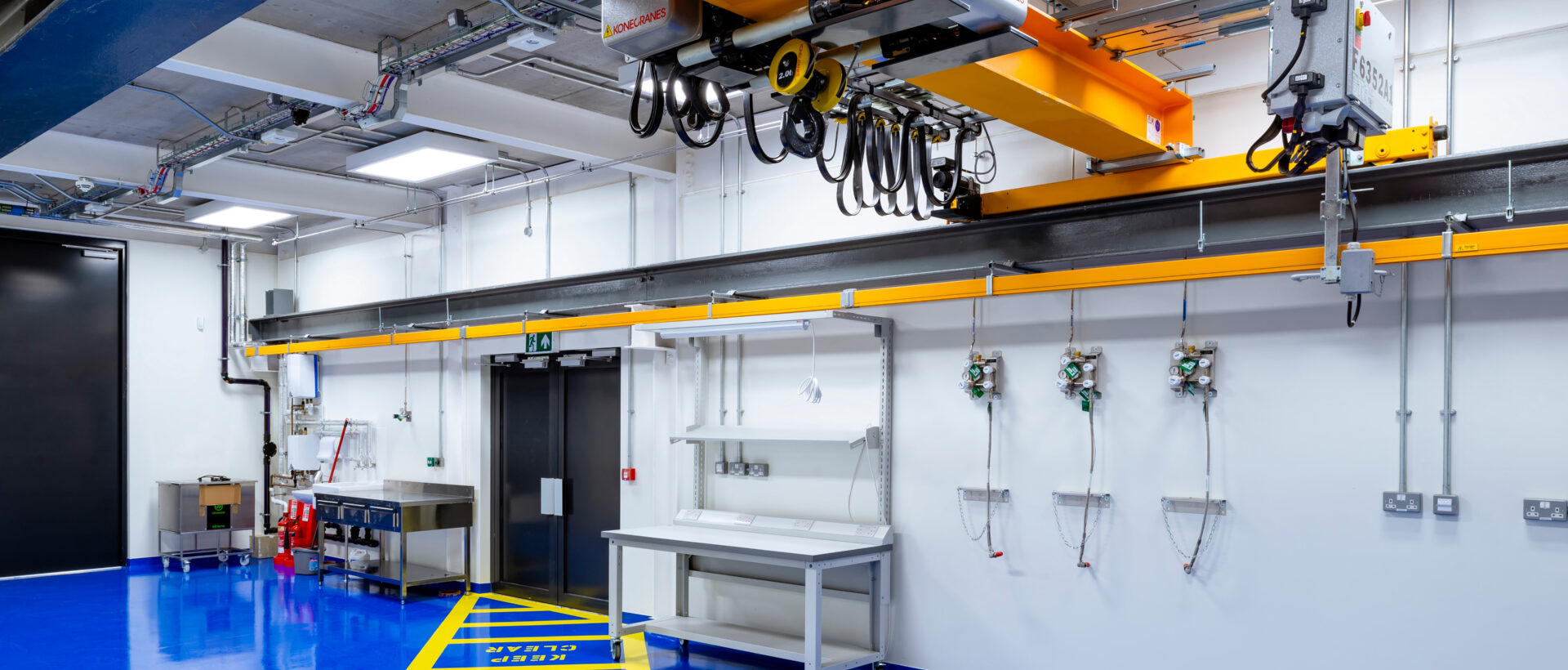
Introduction
With investors keen to take advantage of the life sciences boom in the UK, developers of mixed use schemes are looking at including a life sciences element as a result.
According to research conducted by JLL last year, there is up to £15bn of capital allocated to UK life sciences real estate of which less than 10% has been utilised. Just shy of a quarter (23%) of the £65bn allocated globally for life sciences is in the UK.
Investors who may have had their fingers burnt through investing in other industries during the pandemic want greater security, and ESG impact investors are equally as attracted to the merits of the sector.
Subsequently, developers are looking beyond the pure life sciences facilities in the ‘golden triangle’ of London, Cambridge and Oxford to consider the use of life sciences in mixed use schemes across the country.
Life sciences
Life sciences, by their very nature, have complex requirements that other mixed use scheme elements like office and residential don’t have. Their fit-out includes laboratories, teaching rooms, collaboration spaces, workshops, clean rooms and plant rooms – all with strict compliance and regulations.
Early collaboration with the end user and project team is key to avoiding any nasty surprises down the line. We break it down to three specific areas to give some serious consideration – structure, space and equipment – to give your scheme the best chance of success.
Structure
When it comes to the structural element of a life sciences build, it’s important to get the right floor to ceiling height as there are far more services required than, for example, an office fit-out. Bigger voids are needed to house large duct work, whether that’s in a suspended ceiling or exposed.
Technical areas or plant rooms are typically significant spaces and can stretch along an entire length of lab space or existing in the entire floor above the lab space. This is to ensure efficient capacity of services whether that be HVAC, electrical, BMS or utilities and ensuring close proximity to the space.
Waste disposal is a big consideration as part of the structural element of a life sciences build. Disposal of specimens, samples, and mediums all need proper processes and routes and, in the case of disposal through waste pipework, consideration needs to be given on the materials (e.g., Vulcathene). Outside the building, life science waste might need to be segregated from normal foul waste and all environmental and safety aspects need to be evaluated, i.e., treatment on site or safe removal from site.
The movement of goods around the building needs to be considered, if you’re on an upper floor for instance, what raw materials, finished goods or waste products need to be brought in and out? Is a goods lift needed as well as a personnel one?
Kevin Jones
|Director
|Pulse Consult
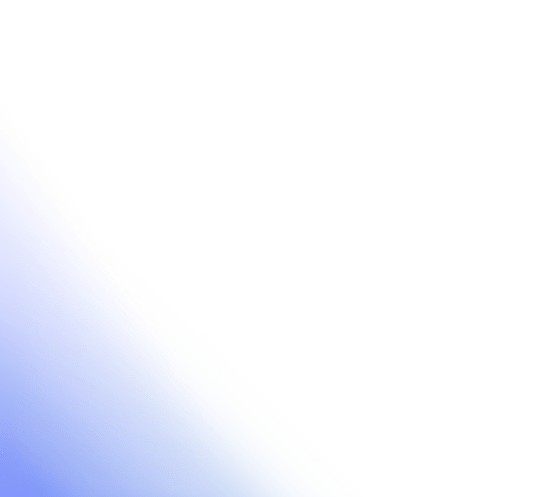
Space
When it comes to life sciences space – the environmental space is just as key a consideration as the physical space. It’s essential to define the environmental grade of spaces like a clean room very early on because this has significant impact on fit-out and technical aspects such as air changes and pressure gradients. If, for example, users are moving between spaces with different environmental grades and bio-safety levels, the air gradient needs to cascade correctly to avoid contamination.
A biological safety level classification has its own requirements and constraints including strict access control, ante rooms, interlocks, decontamination systems and toxic waste disposal and equipment such as biological safety cabinets.
The stringent commissioning and qualification requirements will also add both cost and time to your schedule with each system and process requiring documentation to demonstrate it is performing to pre-defined criteria.
A higher clean room environmental grade means you’ll need HEPA filters fitted to the duct work to capture particles so that grade can be met. HEPA filters are expensive and, when scaled over a significant floor area, the cost soon mounts up.
When fitting out clean spaces, you might want to ask, do partitions, glazing and fittings (e.g., pass through hatches) need to be flush to minimize dust collection.
For life sciences in a mixed used scheme, we’d recommend collaborating with the end user as early as RIBA stage 0 (strategic definition) rather than leave it until RIBA stage 3 (spatial coordination) because space is used so differently to other sectors and they’re the experts in what’s needed. You certainly need gowning and changing areas with showers and lockers – it’s ancillary spaces like these that all place a demand on the available space in a development.
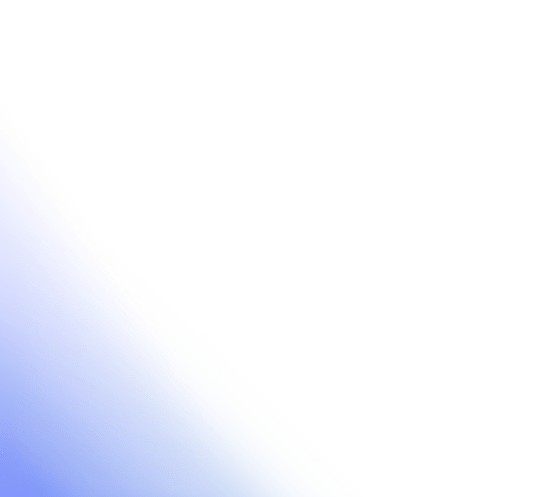
Collaboration spaces – or write-up spaces– tend to adjoin the labs so that users and can dip in and out of each space conveniently and safely. Access controls, with different access levels, to different rooms are also common in life sciences fit-outs. And plant rooms for life sciences tend to be bigger than those in office spaces as they have larger air handling units because the air changes are much greater.
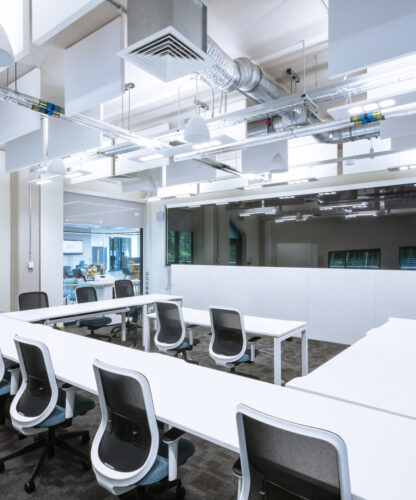
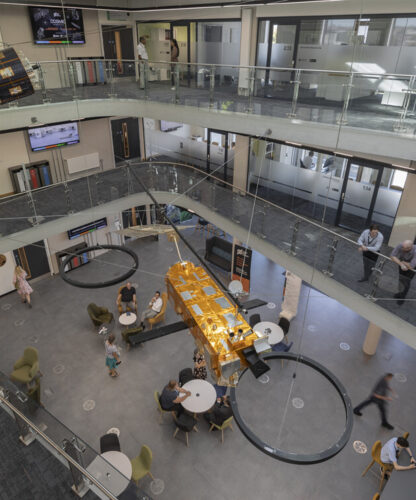
Equipment
It’s highly likely a life sciences build is going to need to house specialist equipment which has an impact on the structure and space. There are multiple considerations when it comes to equipment:
01
Weight
Does the floor need reinforcing?
02
Height
Do you need a pit in the floor or a bulkhead in the ceiling?
03
Size
Do you need special access doors to get the equipment in situ? Is there enough room around it for users to operate it safely?
04
Maintenance
how is the equipment maintained, is it sensitive to vibrations?
05
Power
From where/how is power supplied and at what output?
06
Laboratory gases
Are lab gases like nitrogen, argon, helium and hydrogen required to the area?
07
Cleaning
Do you need a parts washer or autoclave and what services/utilities?
Consideration needs to be given to utilities such as gases, purified water (DI/WFI) or steam and how this is generated (e.g., bottled or generated on site). If there’s nitrogen, then environmental detectors need to be installed to monitor levels of gases in the air as you can’t smell a nitrogen leak.
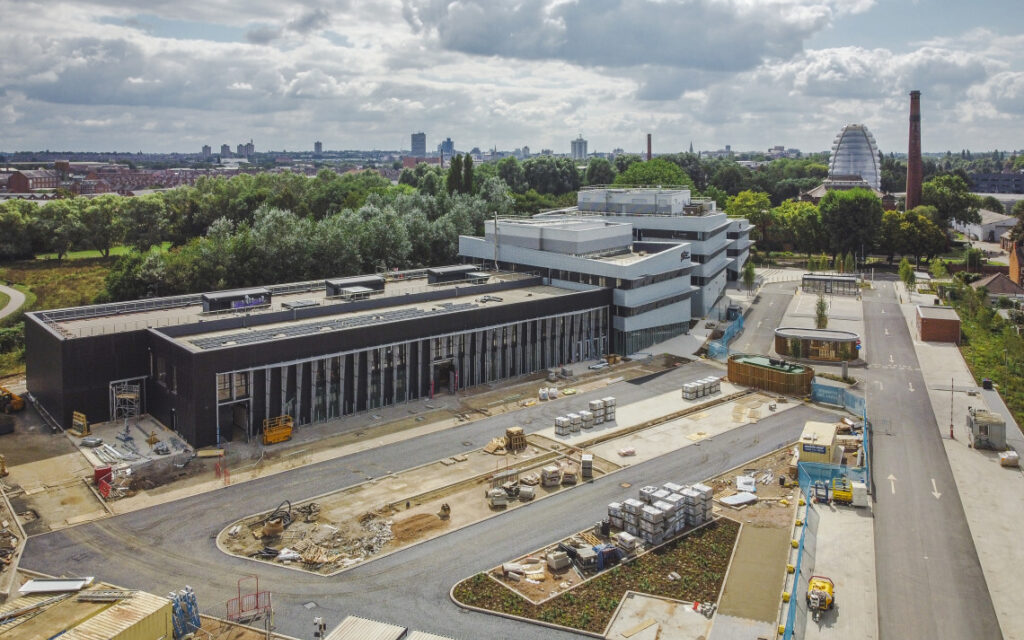
Photo credit - Martine Hamilton Knight for SEH Architects
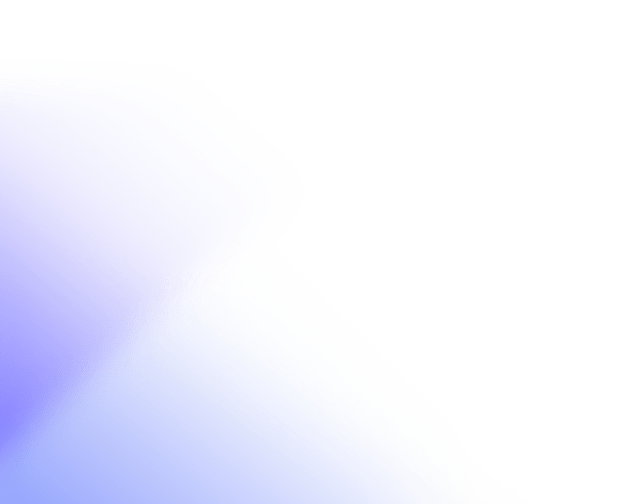
Summary
The requirements for a life sciences as part of a mixed use scheme can be tricky to navigate so early collaboration with the end user right from the offset is key to avoiding costly mistakes and building a building not fit for life sciences’ purpose.
Pulse Consult have over a decade of experience in the life sciences sector including Laboratories, Education, Hospitals, and GMP facilities, small and large.
Get in touch
If you’d like to discuss a project then please get in touch with our director, Kevin Jones.